Volume 4 - Year 2016 - Pages 17-27
DOI: 10.11159/ijtan.2016.003
A Sustainable Route for Antibacterial Nanofinishing of Textiles
Esther Hontañón1, Jörg Meyer2, María Blanes3, Vicente Cambra3, Xiaoai Guo2, Matthias Masuhr1, Alex Muntean2, Laura Santos4, Hermann Nirschl2, Einar Kruis1
1University of Duisburg-Essen, Institute for Technology of Nanostructures
Center for Nanointegration Duisburg-Essen (CENIDE), 81 Bismarckstraße, Duisburg, Germany 47057
esther.hontanon@uni-due.de; einar.kruis@uni-due.de
2Karlsruhe Institute of Technology, Institute for Mechanical Process Engineering and Mechanics
8 Straße am Forum, Karlsruhe, Germany 76131
joerg.meyer@kit.edu; xiaoai.guo@kit.edu; alex.muntean@kit.edu; hermann.nirschl@kit.edu
3AITEX Technological Textile Centre, Department of Technical Finishing and Comfort, General Direction of R&D
Plaza Emilio Sala, Alcoy, Alicante, Spain 0381
mblanes@aitex.es; vcambra@aitex.es
4Foundation for the Promotion of the Textile Industry of the Valencian Community (FOMENTEX)
20 Els Telers, Ontinyent, Valencia, Spain 46870
laura@fomentex.eu
Abstract - In this paper, an aerosol-based process is shown for imparting antibacterial property to textiles. Metal nanoparticles (copper and silver) are produced by means of DC electrical discharges (glow and arc) between two electrodes in nitrogen at ambient pressure and passed through textile fabrics (cotton, polyester and lyocell) which act as filter media. The particle retention efficiency of the fabrics is measured in dependence of particle size and face velocity. The antibacterial performance of the fabrics treated with metal nanoparticles and its durability to wash is assessed according to industry standards. Loads of about 200 ppm (2x10-2 %wt.) of nanoparticles of copper or silver give strong antibacterial property but the colour and hand feeling of the fabrics are significantly affected. Nanosilver loads in the order of 50 ppm (5x10-3 %wt.) impart comparably high antibacterial property to the fabrics with no visible impact on colour and hand touching, and wash fastness is proven for 10 washes. Small silver nanoparticles (<5 nm) result in much less release of silver to wash water, with respect to larger nanoparticles (>20 nm).
Keywords: Textile nanofinishing, metal nanoparticles, electrical discharges, aerosol filtration, antibacterial activity
© Copyright 2016 Authors - This is an Open Access article published under the Creative Commons Attribution License terms. Unrestricted use, distribution, and reproduction in any medium are permitted, provided the original work is properly cited.
Date Received: 2015-09-19
Date Accepted: 2015-07-04
Date Published: 2016-09-07
1. Introduction
Numerous types of nanomaterials have been developed in recent years for use as antimicrobial agents in textiles [1], [2]. Among them, silver nanoparticles (NP) have proved to be the most effective against a large variety of microorganisms [3], [4] and, thus, the use of antimicrobial nanosilver in functional textiles is being explored for many high-performance applications such as protective clothing; medical, biomedical and healthcare textiles; industrial filtration and others [5]. In addition, copper is relatively stable in terms of both chemical and physical properties and cheaper than silver. A few studies have reported the antibacterial properties of copper NP. They show nanocopper offers significant promise as antibacterial agent [6], [7], also when supported on textiles [8], [9]. NP are applied to textiles in form of nanofinishings and nanocoatings, relying on dispersions of the active NP that are generated by using chemical precursors in solvents including surfactants, stabilizers and binders. NP are applied from the dispersions onto the textiles most commonly by a dip-pad-dry-cure method which has several drawbacks [10], [11]. Chemicals are expensive and drying and curing incur high energy consumption and increase costs. The dispersions lead to effluents carrying harmful substances and NP, thereby enhancing water waste treatment costs. Besides, surfactants cover the nanoparticle surface reducing its activity, and polymeric stabilizers and binders degrade air permeability and lead to stiffer hand feeling of textiles treated with NP.
An aerosol-based process is described and its feasibility for antibacterial nanofinishing of textiles is explored here. Metal NP are produced by evaporating an electrode by means of DC electrical discharges, namely glow discharge and arc discharge, in an inert gas at atmospheric pressure. The NP are carried in a gas flow through the textile fabric where they are partially retained. Electrical discharges in gases have recently gained attention as a sustainable, easy to use and flexible technique for the synthesis of metallic NP [12], [13]. Furthermore, arc discharge is suited to mass production of metal NP because of its simplicity and high energy efficiency, as compared to techniques currently used for industrial production of NP, and also power supplies to drive arc are commercially available at affordable prices. This makes it possible to scale up nanoparticle production by using multiple electrodes in parallel [14]. Particle retention in fibrous media has been studied since the 60s, mostly in relation with industrial gas cleaning and air purification, and the mechanisms causing particle deposition and attachment to fibres are well-known [15], [16]. Diffusion is the leading deposition mechanism for NP and the capture efficiency increases with decreasing fibre diameter, particle size and face velocity (gas flow rate / surface area of the fabric exposed to the flow). Then, retention of particles in fibrous media depends upon the particle collection efficiency of the fibres and the thickness, porosity and fibrous structure of the medium.
In this work, aerosol filtration is assessed for three commonly used textile fabrics, namely cotton, polyester and lyocell. These show particle retention fractions relevant to nanofinishing of textiles, especially for highly diffusive NP (<10 nm). Then, aerosols of copper and silver NP are produced by means of electrical discharges in nitrogen and passed through the fabrics where particles are retained. Finally, the antibacterial activity of the fabrics treated with NP and the release of silver from the fabrics during washing are determined following industry standards.
The aerosol route presented here may be a sustainable cost-effective alternative to wet routes currently used for nanofinishing of textiles in the industry. NP generation and application of NP to textiles rely on simple scalable processes. Furthermore, neither chemicals nor solvents are used and, hence, hazardous effluents are not delivered. Finally, as long as the system is tight and the gas is recycled, NP are not released either to the work place or the environment.
2. Experimental
2.1. Methods
Figure 1 shows a sketch of the setup used in this work for applying metal NP from the gas phase onto textiles. It consists of an aerosol generator (reactor) followed by a round hollow HEPA filter enclosed in a housing (filtration chamber). The inner surface of the filter is covered with a sample of a textile fabric. A fraction of the aerosol particles deposit in the fabric, while particles passing through the fabric are retained in the HEPA filter. The clean gas is then directed either to the exhaust or back to the reactor (recirculation mode), depending upon the gas flow rate. The system is tight; it is evacuated (10-5 mbar) and then filled up with the working gas before starting any experiment.
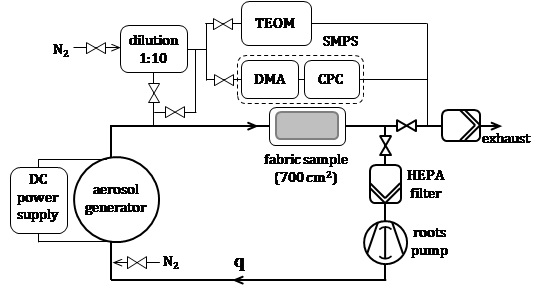
In the reactor, a metal electrode is evaporated by means of an electrical discharge in inert gas at ambient pressure. The discharge is driven by a DC power supply whose technical characteristics depend upon the type of discharge; this is glow discharge at currents below 1 A and arc discharge at currents beyond 10 A. NP form by nucleation and condensation of the metal vapour in the discharge zone and evolve further due to processes like particle coalescence, coagulation and sintering. The reactor and the power supply, as well as the aerosol mass production rate and particle size distribution (PSD) have been described elsewhere (cf. [12], [17] for glow discharge and [13], [18] for arc discharge).
Downstream of the reactor the aerosol passes through the textile fabric. A fraction of the particles deposit onto the fabric fibres, whereas penetrating particles are retained by the following HEPA filters. In this work, particle retention in textile fabrics is measured in dependence of particle size and face velocity. To that aim, a second setup (Figure 2) is used, enabling precise control over the size and morphology of the particles used for the measurements.
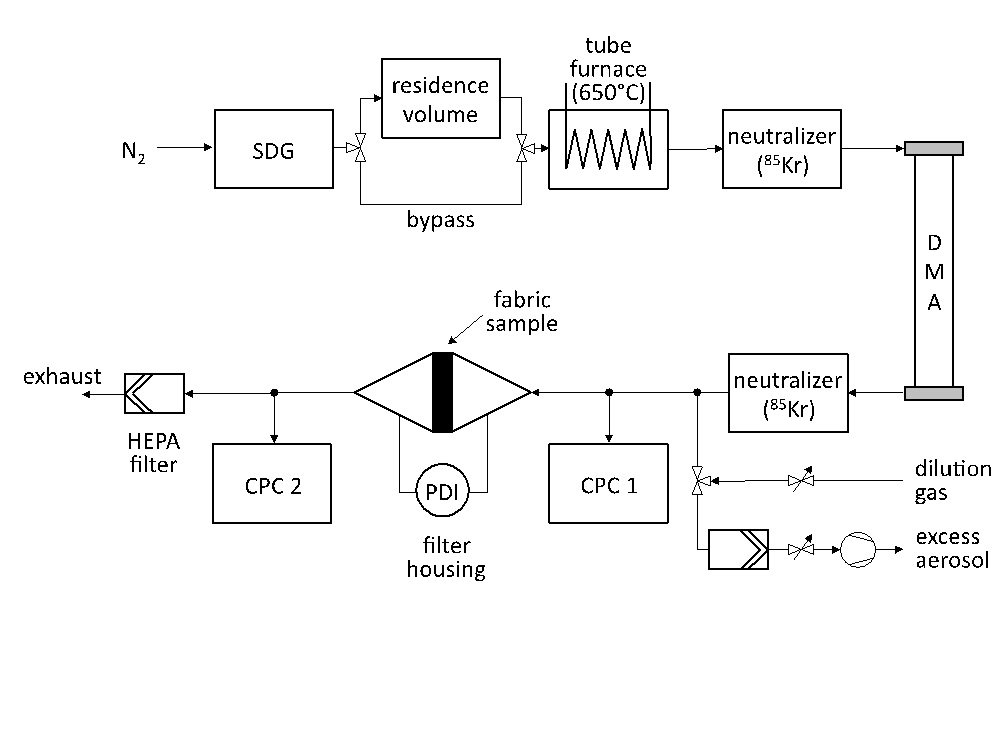
Silver NP are synthesized in a spark discharge generator (SDG). Depending upon the target particle size, the aerosol either passes a residence volume for further agglomeration to attain large particles or bypasses this volume to proceed with the small agglomerates leaving the SDG. Subsequently, the aerosol is feed through a tube furnace to form compact spherical particles (sintering). The spheres are neutralized (bipolar 85Kr charger) and size classified by using a differential mobility analyzer (DMA). The aerosol leaving the DMA is again neutralized to reduce the effect of multiple charged particles on collection efficiency. The aerosol flow rate is then adjusted to the desired face velocity by either removing excess aerosol or mixing the aerosol with a defined flow rate of a clean dilution gas. The retention efficiency measurement is performed on a small fabric sample (active surface area 14 cm2) placed in a filter holder, by measuring the aerosol particle number concentration upstream and downstream of the fabric sample with two condensation particle counters (CPC 3775, TSI Inc., USA) simultaneously.
The flow pressure drop across the fabric sample is measured by a handheld differential pressure transducer (521, Testo AG, Germany). No increase of the pressure drop is detected in the measurements.
2.2. Measurement techniques
The aerosol exiting the reactor is continuously monitored in the experiments. A tampered element oscillating microbalance (TEOM 1405, Thermo Fisher Scientific Inc., USA) measures the mass production rate, while the PSD is measured by means of a scanning mobility particle sizer (SMPS 3080, TSI) including a differential mobility analyzer (DMA 3085 / 3081, TSI) and a condensation particle counter (CPC 3775, TSI). High-density aerosols obtained by arc discharge are diluted (VLK 10, Palas GmbH, Germany) by adding a flow of a clean gas (N2) to the aerosol flow (dilution ratio 1:10) upstream of the measurement instruments.
After the experiment, small pieces (~ 1 cm2) are cut from the large fabric sample (active surface area 700 cm2) treated with metal NP and analyzed by scanning electron microscopy (SEM). The remaining sample is used to assess the antibacterial performance of the fabric including durability to washing and the release of silver from the fabric. International standards used in the industry serve that purpose. A quantitative absorption method is used to measure the antibacterial activity of the fabrics following ISO 20743:2013 [19]. The load of metal in the fabric is evaluated by means of a microwave acid digestion method according to OEKO-TEX â 100 [20], while the release of metal is determined by washing of the fabrics in a laboratory washing machine (Linitest, SDL Atlas, UK) conforming to ISO 105 C06:2010 [21]. The content of silver in the digestion solution and the wash water is measured by inductively coupled plasma-mass spectrometry (ICP-MS).
2.3. Materials
The materials used for NP synthesis are two metal electrodes and an inert gas. The evaporating electrode is a rod (glow discharge) or shots (arc discharge) of a few mm in size, and the counter-electrode is a tungsten wire (Æ 1.6 mm). High purity electrodes (>99.99%) of copper, silver and tungsten are used and the carrier gas is pure nitrogen (99.999%).
Table 1 shows a list of the textile materials used in this work. They differ in the origin of the fibres as well as in the thickness, weight and fibrous structure. SEM images of the textiles are displayed in Figure 3. They show the side of the fabric facing the aerosol flow in the experiments (front side). As can be seen, the fabrics consist of microfibers of 10-20 m in diameter being aligned and grouped in bundles which are interlaced with each other and form ordered patterns.
Table 1. Textiles used in this work.
Fabric (Acronym) | Cotton (CT) | Polyester (PS) | Lyocell-1 (LC1) | Lyocell-2 (LC2) |
Area weight (g/m2) | 150 | 200 | 225 | 130 |
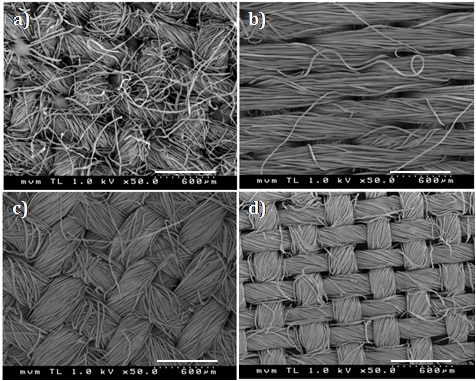
3. Results
3.1. Particle collection efficiency
The measured particle collection efficiencies are shown in Figure 4 for the four fabrics, particle sizes from 10 nm to 150 nm and face velocities from 0.5 cm/s to 4 cm/s. The measured efficiencies represent initial efficiencies, as the loading of the fabrics remained quite low (<0.2% of a monolayer of particles). The error of collection efficiency data is 10% (CPC). For all fabrics the collection efficiency increases with decreasing particle size and face velocity, as expected for the diffusional deposition regime [15], [16].
For particles larger than 20 nm, the collection efficiency stays below 50% for CT, LC1 and LC2 fabrics, and levels off in the range of 10% and below for the largest particles of 150 nm. These fabrics can then be used to efficiently deposit small NP less than 10 nm, especially at low face velocity. Yet, even at face velocities as low as 0.5 cm/s, significant penetration occurs (25-40%), leading to high losses of active NP. These losses can be reduced, if multiple layers of the fabric are used for coating.
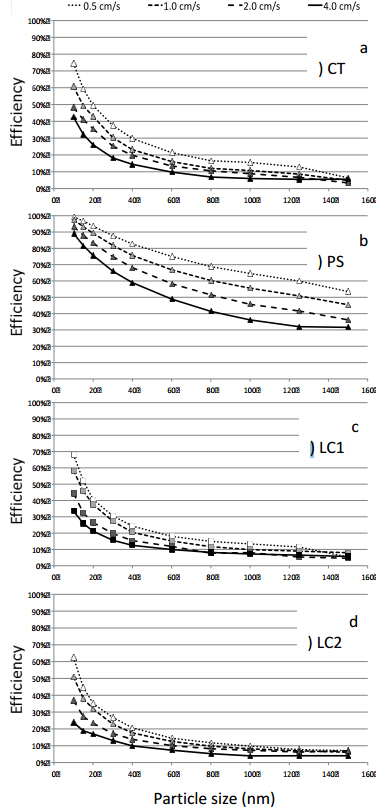
The PS fabric shows the highest particle collection efficiency over the whole particle size range. For 10 nm particles deposited at the lowest face velocity of 0.5 cm/s particle retention is almost complete (>99%). Even at the high face velocity of 4 cm/s, penetration is in the order of 10%, allowing for efficient collection with a single fabric layer. Also, for a given particle size, the retention efficiency of PS fabric varies largely with face velocity, and this variation widens with increasing particle size (Figure 4b), contrary to the tendency observed for the other fabrics (Figures 4a, c, d).
The different filtration behaviour of the PS fabric, with respect to CT and LC fabrics, is attributed to the different weaving structure of the PS fibres. While CT and LC fabrics show a lot of rectangular fibre crossings with a high tendency to form pinholes (small channels between crossings of fibre pairs, clearly visible in Figures 3a and 3d), PS fabric shows a smoother surface consisting of parallel multifilament threads with higher porosities within the individual fibre bundles. Overall, this results in a fibre layer with more homogeneous permeability and less pinholes, which is strongly preferable for efficient particle collection.
The homogeneity of particle deposition over the fabric depth is also related to the collection efficiency of the fabric. At low collection efficiencies, the particle concentrations in the front and back sides of the fabric differ only slightly from each other. Then, the inlet particle concentration and, thus, the diffusional flux of particles to the fibres stay almost constant over the fabric depth, resulting in bulk deposition. However, at high collection efficiencies the particle concentration in the aerosol drops by an order of magnitude over the fabric depth. It means that there are almost no particles left to deposit on the back side of the fabric, resulting in a kind of surface deposition on the front side.
Therefore, surface coating is favoured by high collection efficiency fabrics, small particles and low face velocities, while bulk deposition is preferential for low collection efficiency fabrics, large particles and high face velocities. Furthermore, due to the inhomogeneity of the weaving fibrous structure, deposition within a plane at a given depth will never be homogeneous.
3.2. Antibacterial activity and silver release
3.2.1. Glow discharge
Firstly, NP of copper and silver are generated by high current glow discharge (0.6 A) and applied to cotton fabric. The most relevant conditions of the aerosol process are summarized in Table 2. The gas flow rate is a key parameter, since it determines the agglomeration degree of the aerosol particles. Besides, the face velocity influences the particle collection efficiency of the fabrics, as discussed in the section 3.1.
Table 2. Deposition of metal NP (high current glow) on cotton fabric by aerosol filtration. NP load and antibacterial activity of cotton fabric treated with metal NP.
Sample | CT1 | CT2 | CT3 | CT4 | |
Metal | Cu | Cu | Ag | Ag | |
Glow current (A) | 0.6 | 0.6 | 0.6 | 0.6 | |
Flow rate (lpm) | 500 | 100 | 500 | 500 | |
Prod. rate (mg/h) | 5-10 | 5-10 | 0.5 | 0.5 | |
PSD mode (nm) | 10 | 80 | 7 | 7 | |
Face velocity (cm/s) | 12 | 2.4 | 12 | 12 | |
Duration (h) | 1 | 2.5 | 1 | 4 | |
NP* load (ppm) | 100-200 | 125-250 | 25 | 100 | |
Antibacterial activity | SA | 4.5 | 4.5 | 4.7 | 4.7 |
KP | 4.5 | 4.5 | 2.5 | 4.7 |
* NP load is given as aerosol production rate (TEOM) x particle collection efficiency of cotton fabric (Figure 4a) x duration of the experiment.
In the experiments with copper the aerosol production rate varies between 5 mg/h and 10 mg/h (TEOM). Figure 5a displays the PSD of the copper aerosols (SMPS) at the inlet of the filtration chamber. The PSD mode stays at 10 nm in the experiment at a flow rate of 500 lpm and at 80 nm in the experiment at a flow rate of 100 lpm. SEM images of copper NP deposited on cotton fabric are shown too. In Figure 5b, an even layer of individual NP less than 30 nm (primary particles) is observed in the sample treated at the high gas flow rate (CT1), while in Figure 5c lower coverage and larger agglomerates are found in the sample treated at the low flow rate (CT2). These findings are in accordance with the PSD of the aerosols in Figure 5a. The inserts in the SEM images are pictures of the cotton samples treated with copper NP. The colour of the fabric turns light grey and dark grey in the experiments at flow rates of 500 lpm and 100 lpm, respectively.
A rough estimation of the load of copper in the cotton samples is obtained as the product of the aerosol production rate, the collection efficiency of the fabric for particles of a size equal to the mode of the aerosol PSD at the given face velocity, and the exposure time of the fabric to the aerosol. The error of metal load data is 20% (TEOM). It is assumed (Figure 4a) that the cotton retention efficiency is of 20% at 500 lpm (10 nm, 12 cm/s) and of 10% at 100 lpm (80 nm, 2.4 cm/s). These lead to copper loads of 100-200 ppm in the sample finished at 500 lpm (CT1) and 125-250 ppm in the sample treated at 100 lpm (CT2). The darker colour of CT2 is due to large agglomerates mostly retained in a thin layer in the front side of the fabric, while small NP deposit over the entire depth of the fabric.
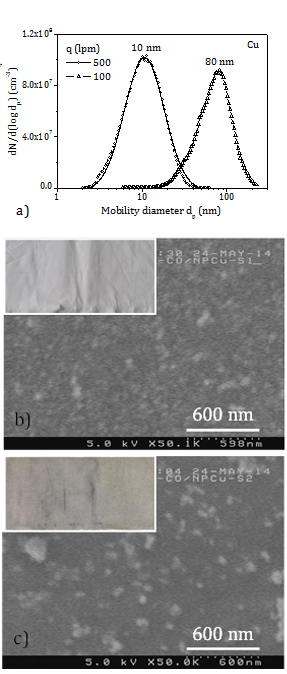
The antibacterial activity of cotton samples with copper NP is assessed against ,i>Staphylococcus aureus (SA) and Klebsiella pneumoniae (KP) in compliance with ISO 20743. This establishes the following rank for antibacterial activity: (logarithmic) values below 2 are not meaningful; values between 2 and 3 indicate acceptable antibacterial performance; and values above 3 reveal strong antibacterial property. The CT1 and CT2 samples attain high antibacterial activity for SA and KP (4.5). The data uncertainty varies from 10% to 30%.
It is well-known that silver is a more efficient antibacterial agent than copper. Besides, at a given glow current, lower evaporation rate and smaller primary particles are attained for silver, enabling higher surface area for bacteria attachment. Then, two experiments are carried out with a silver electrode at high glow current (0.6 A) and high gas flow rate (500 lpm) for 1 h and 4 h duration, respectively. Aerosol production is in the order of 0.5 mg/h and particles are smaller than 15 nm with mode at nearly 7 nm, as shown in Figure 6.
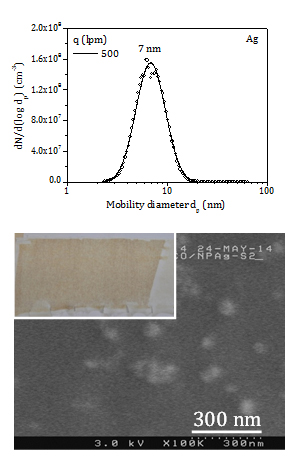
The colour of cotton changes to light brown and dark brown after 1 h (CT3) and 4 h (CT4) filtration. Assuming a collection efficiency of 50% (7 nm, 12 cm/s) the load of silver NP is roughly 25 ppm and 100 ppm in the CT3 and CT4 samples. A SEM micrograph of the CT4 sample is displayed in Figure 6. Few individual NP and agglomerates scarcely dispersed on the surface of the fibres are observed. It is noted that most particles are smaller than 10 nm, rendering their observation quite difficult (the detection limit of our SEM is 10 nm).
The CT3 and CT4 samples reach high antibacterial activity against both bacteria (4.7), except for CT3 which shows lower antibacterial activity for KP (2.5).
By reducing the glow current, both the electrode evaporation rate and the primary particle size diminish. At a current of 0.4 A, aerosol production falls down to values not measurable with the TEOM and particles are mostly nanoclusters less than 5 nm, hardly detectable by using the SMPS (detection limit 3 nm). Filtration experiments are then carried out with polyester fabric and silver NP generated by low current glow; the process conditions are compiled in Table 3.
Changes in the colour of polyester fabric are hardly (pale brown) or not visible at all. Likewise, NP are just barely seen on the fibres due to the lack of resolving power of the SEM.
Table 3. Deposition of silver NP (low current glow) on polyester fabric by aerosol filtration. Antibacterial activity of the polyester fabric treated with silver NP.
Sample | PS1 | PS2 | PS3 | PS4 | PS5 | PS6 | PS7 | PS8 | |
Metal | Ag | ||||||||
Glow current (A) | 0.4 | 0.4 | 0.2 | 0.2 | 0.2 | 0.2 | 0.3 | 0.2 | |
Flow rate (lpm) | 25 | 25 | 50 | 100 | 100 | 100 | 100 | 100 | |
Prod. rate* (mg/h) | < 0.1 | ||||||||
PSD mode* (nm) | < 5 | ||||||||
Face velocity (cm/s) | 0.6 | 0.6 | 1.2 | 2.4 | 2.4 | 2.4 | 2.4 | 2.4 | |
Duration (h) | 1.5 | 4 | 1 | 5.5 | 8 | 1 | 2 | 3 | |
Antibact. activity | SA | 5.4 | 4.6 | 2.6 | 4.6 | 1.9 | 2.7 | 5.4 | 5.4 |
KP | 3.5 | 5.1 | 5.1 | 5.1 | 5.1 | 4.0 | 5.1 | 5.1 |
* Production rate and PSD mode are below the detection limit of TEOM and SMPS, respectively.
The values of the antibacterial activity attained by polyester fabric samples containing silver NP are displayed in Figure 7. They correspond to as-prepared samples and after washing in a domestic wash machine (PS1, PS2, PS7 and PS8 up to 10 washes). The antibacterial activity of the cotton samples treated with copper NP (CT1, CT2) and with silver NP (CT3, CT4) in the previous experiments is shown also for comparison.
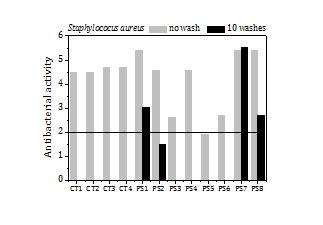
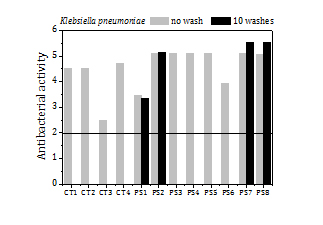
As can be seen in Figure 7, all polyester samples exhibit strong antibacterial activity against KP, with values ranging from 3.5 to 5.1, and it maintains after 10 washes. The antibacterial activity against SA is also good. The values vary between 2.6 and 5.4, except for PS5 whose antibacterial activity lies slightly below the threshold (2). The antibacterial activity against SA, however, reduces after 10 washes, except for PS7. The load of silver in the polyester samples is much lower than the load of copper and silver in the cotton samples, and particles are also smaller. The former, however, reaches higher antibacterial activity and also silver does not have any perceptible effect on the colour and hand feeling of the polyester fabric.
The load of silver (ECO-TEXâ 100) and the release of silver in the first wash (ISO 105C06) are measured for PS1 and PS4 fabric samples. The results are shown in Table 4. The error of the data is about 8% (ICP-MS). The release of silver from PS1 and PS4 samples in the first wash (1.3%) is noticeably lower than the release of silver from textiles containing commercial nanosilver applied by pad-dry route (e.g. 8-10% release is reported in [22] for silver NP of mean size less than 20 nm).
Table 4. Silver load and silver release in the first wash of polyester fabric treated with silver NP.
Sample | Ag load (ppm) | Ag release 1st wash | |
(ppm) | (%) | ||
PS1 | 40 | 0.50 | 1.26 |
PS4 | 61 | 0.83 | 1.36 |
Therefore, silver nanoclusters (<5 nm) produced by low current glow and applied by aerosol filtration may impart durable antibacterial property to textiles. However, the time it takes to reach the necessary load of silver is too long (>1 h). NP production can be enhanced by using multiple electrodes in parallel, but this is not affordable, as power supplies to drive glow discharge are costly (>5.000 €). Moreover, toxicological studies have shown silver NP less than 10 nm may significantly enhance the risk to human health and environment [23], [24], thus, posing a serious concern to the use of nanosilver in consumer goods.
3.2.2. Arc discharge
It may be then worth to enhance the production of larger silver NP (>20 nm) to speed up nanofinishing of textiles and to reduce the life cycle impact of textiles containing nanosilver. To that aim, experiments are conducted with the reactor operating in arc mode at the lowest current ensuring continuous stable production of silver aerosol (15 A) and a nitrogen flow rate of 40 lpm, as summarized in Table 5. The production rate of silver NP varies between 40 mg/s and 60 mg/s. Samples of cotton, polyester and lyocell fabrics are exposed to the aerosol from less than 1 minute up to 10 minutes.
Figure 8 displays the PSD of the silver aerosols and a SEM micrograph of the surface of the fibres of the sample CT1. NP together with a few particles and agglomerates larger than 100 nm are distinguished in the image. The CT1 and CT2 cotton samples turn grey after the experiments, while changes in colour are not visible for any other fabric sample.
The load of silver, the release of silver by washing and the antibacterial activity of the fabrics before washing and after 3 washes (Figure 9) are summed up in Table 5 too. The fabrics exhibit a high antibacterial activity against SA (5.6) over a broad range of silver loads, from 15 ppm to 200 ppm. Fabrics with silver loads above 50 ppm show also strong antibacterial activity against KP (5.4) and it reduces to 1.6-2.5 for silver loads below 50 ppm.
Table 5. Deposition of silver NP (low current arc) onto textile fabrics (cotton, polyester and lyocell) by aerosol filtration. Silver load, release of silver by washing and antibacterial activity of the fabrics before washing and after 3 washes.
Arc current (A) | 15 | ||||
Flow rate (lpm) | 40 | ||||
Production rate (mg/h) | 40-60 | ||||
PSD mode (nm) | 40-50 | ||||
Face velocity (cm/s) | 1 | ||||
Duration (min) | 0.33-10 | ||||
Sample | CT1 | CT2 | PS1 | PS2 | |
Ag load (ppm) | 200 | 186 | 77 | 65 | |
Antibacterial activity | SA | 5.6 | 5.6 | 5.6 | 5.6 |
KP | 5.4 | 5.4 | 2.5 | 5.4 | |
Ag release (ppm): | |||||
1st wash | 65.4 (32.7%) | 32.3 (17.4%) | 4.3 (5.6%) | 3.2 (5.0%) | |
2nd wash | 19.3 (9.7%) | 1.3 0.7%) | 1.4 (1.8%) | 0.9 (1.4%) | |
3rd wash | 1.6 (0.8%) | 0.9 (0.5%) | 1.4 (1.8%) | 0.9 (1.4%) | |
Antibacterial activity (after 3rd wash) | SA | 5.5 | 5.5 | 0.4 | 5.5 |
KP | 5.5 | 5.5 | 5.4 | 5.5 | |
Sample | LC1.1 | LC1.2 | LC2.1 | LC2.2 | |
Ag load (ppm) | 15 | 35 | 15 | 51 | |
Antibacterial activity | SA | 5.6 | 5.6 | 5.6 | 5.6 |
KP | 5.4 | 5.4 | 1.6 | 2.5 | |
Ag release (ppm): | |||||
1st wash | 1.6 (10.9%) | 7.4 (21.0%) | 3.6 (24.0%) | 15.0 (29.4%) | |
2nd wash | 0.7 (4.6%) | 0.7 (2.2%) | 0.9 (6.2%) | 1.2 (2.3%) | |
3rd wash | 0.7 (4.6%) | 0.5 (1.4%) | 0.9 (6.2%) | 1.2 (2.3%) | |
Antibacterial activity (after 3rd wash) | SA | 4.2 | 5.5 | 5.5 | 5.5 |
KP | 5.5 | 5.5 | 5.5 | 5.5 |
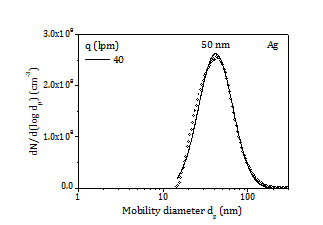
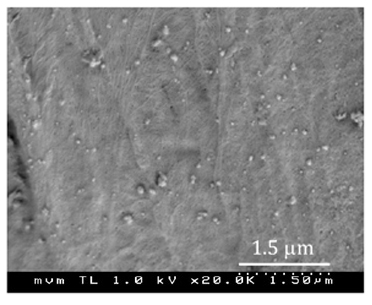
The fraction of silver released to the water in the first wash is remarkably high for all samples (5-33%). In the second and third washes the fraction of silver that goes to the water diminishes significantly, to values about or even below 2%. The high antibacterial activity of the fabrics remains the same or even increases (e.g. PS1 and LC2 fabric samples against KP) after 3 washes.
We attribute the release of silver from the fabrics in the first wash to large particles and agglomerates (Figure 8, SEM) weakly adhered to the fabric fibres. Particles of 200 nm and bigger are commonly observed in aerosols from arc sources; they form by “splashing” of molten metal from the crucible containing the evaporating electrode. A few of such large particles may largely contribute to the mass load of silver in the fabric, while they are not much effective as antibacterial agent due to their lower surface area to volume ratio, as compared to NP.
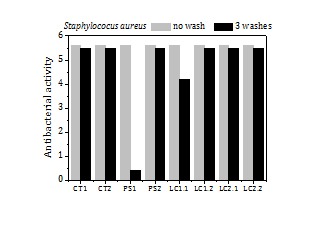
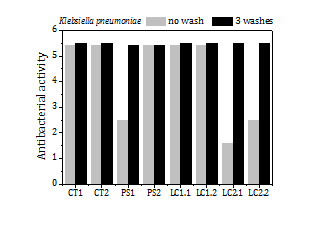
4. Conclusion
A sustainable aerosol process has been explored as to impart durable antibacterial property to textiles. NP of copper and silver have been produced by means of DC electrical discharges and applied to textile fabrics by aerosol filtration. Loads of silver around 50 ppm (5x10-3 %wt.) are proven to give strong antibacterial property regardless of particle size and bacteria type, with no observable effect on the colour and hand feeling of the textile fabrics. Low release of silver to wash water (first wash) and durability of antibacterial property to wash (10 washes) are proven for cotton fabric doped with silver nanoclusters (<5 nm).
Arc discharge is a suitable choice as aerosol source for scaling-up textile nanofinishing, enabling acceptably high production rates over a wide range of particle sizes by tuning the arc current and/or the carrier gas. Nonetheless, large splash particles need to be avoided or removed from the aerosol (e.g. by using a cyclone at the outlet of the reactor) since they easily release into wash water; thus, increasing the risk to human health and environment.
Wash fastness of antibacterial property will be further investigated in a future work, also with regard to the release of silver from the fabric. This will be addressed for large NP (>20 nm) as well as for small NP (<10 nm) produced by arc discharge in nitrogen and argon, respectively.
Finally, there is a need to gain scientific knowledge and fundamental understanding of the antibacterial behaviour of textiles finished with NP by means of dry aerosol routes. In this regard, particle adhesion to textile fibres emerges as a new research topic.
Acknowledgements
This research work has been financially supported by the European Union´s Seventh Framework Program (EU FP7) under Grant Agreement No. 280765 (BUONAPART-E).
References
[1] R. Nayak, and R. Padhye, “Antimicrobial finishes for textiles” in Functional finishes for textiles: Improving comfort, performance and protection, 1st ed., MA, USA, 2015, pp. 361-387. View Book
[2] A. Zille, L. Almeida, T. Amorim, N. Carneiro, M. Esteves, C. Silva and A. Souto, "Application of nanotechnology in antimicrobial finishing of biomedical textiles", Materials Research Express, vol. 1, no. 3, pp. 38, 2014. View Article
[3] S. Prabhu, and E. Poulose, “Silver NP: mechanism of antimicrobial action, synthesis, medical applications and toxicity effects”, International Nano Letters, vol. 2, no. 32, pp. 10, 2012. View Article
[4] M. Rai, A. Yadav, and A. Gade, “Silver NP as a new generation of antimicrobials”, Biotechnology Advances, vol. 27, no. 1, pp. 76-83, 2009.View Article
[5] C. Lawrence, High Performance Textiles and Their Applications, 1st ed., Cambridge, Elsevier, 2014. View Book
[6] M. Usman, M. El Zowataly, K. Shameli, N. Zainuddin, M. Salama, and N. Ibrahim, “Synthesis, characterization, and antimicrobial properties of copper NP”, International Journal of Nanomedicine, vol. 8, no. 1, pp. 4467-4479, 2013. View Article
[7] T. Theivasanthi, and M. Alagar. (2015, Sept. 3). Studies of copper nanoparticle effects on micro-organisms, (2011) [Online]. Available: http://arxiv.org/abs/1110.1372v1
[8] M. Teli, and J. Sheikh, “Modified bamboo rayon-copper NP composites as antibacterial textiles”, International Journal of Biological Macromolecules, vol. 61, pp. 302-307, 2013. View Article
[9] Fars News Agency. (2015, Sept. 3). Silver replaced with copper NP to produce antibacterial fabrics. [Online]. Available: http://english.farsnews.com/newstext.aspx?nn=13930603000129
[10] R. Mishra, J. Militky, V. Baheti, J. Huang, B. Kale, M. Venkataraman, V. Bele, V. Arumugam, G. Zhu, and Y. Wang, “The production, characterization and applications of NP in the textile industry”, Textile Progress, vol. 46, no. 2, pp. 133-226, 2014. View Article
[11] M. Joshi, and A. Bhattacharyya, “Nanotechnology – a new route to high performance functional textiles”,Textile Progress, vol. 43, no. 3, pp. 155-233, 2011. View Article
[12] E. Hontañón, J Palomares, X. Guo, R. Engeln, H. Nirschl, and F. Kruis, “The transition from spark to arc discharge and its implications with respect to nanoparticle production”, Journal of Nanoparticle Research, vol. 15, no. 9, pp. 19, 2013. View Article
[13] M. Stein, D. Kiesler, and F. Kruis, “Effect of carrier gas composition on transferred arc metal nanoparticle synthesis”, Journal of Nanoparticle Research, vol. 15, no. 1, pp. 14, 2013. View Article
[14] M. Stein, and F. Kruis, “Scale-up of metal nanoparticle production”, in Proceedings of Nanotech Advanced Materials and Applications, Washington DC, 2015.
[15] S. Friedlander, Smoke, Dust, and Haze: Fundamentals Of Aerosol Dynamics, 2nd ed., NY, Oxford University Press, 2000.View Book
[16] R. Brown, “Air filtration: an integrated approach to the theory and applications of fibrous filters”, 1st ed., Oxford, UK, Pergamon Press, 1993. View Book
[17] E. Hontañón, J. Palomares, X. Guo, R. Engeln, H. Nirschl, and F. Kruis, “Influence of the interelectrode distance on the production of NP by means of atmospheric pressure inert gas dc glow discharge”, Journal of Physics D: Applied Physics, vol. 47, no. 41, pp. 12, 2014. View Article
[18] M. Stein, D. Kiesler, and F. Kruis, “Adjustment and online determination of primary particle size in transferred arc synthesis of copper NP”, Aerosol Science and Technology, vol. 47, no. 11, pp. 1276-1284, 2013. View Article
[19] ISO 20743:2013 (2015, Aug. 31). Determination of antibacterial activity of textile products. [Online]. Available: https://www.iso.org/obp/ui/#iso:std:iso:20743:ed-2:v1:en
[20] OEKO-TEXâ Standard 100. (2015, Aug. 31). [Online]. Available: https://www.oeko-tex.com/en/business/certifications_and_services/ots_100/ots_100_start.xhtml
[21] ISO 105 C06:2010 (2015, Aug. 31). Colour fastness to domestic and commercial laundering. [Online]. Available: http://www.iso.org/iso/catalogue_detail.htm?csnumber=51276
[22] D. Mitrano, E. Rimmele, A. Wichser, R. Erni, M. Height, and B. Nowack, “Presence of NP in wash water from conventional silver and nano-silver textiles“, ACS Nano, vol. 8, no. 7, pp. 7208-7219, 2014. View Article
[23] A. Gliga, S. Skoglund, I. Wallinder, B. Fadeel, and H. Karlsson, “Size dependent cytotoxixity of silver NP in human lung cells: the role of cellular uptake, agglomeration and Ag release”, Particle and Fibre Toxicology, vol. 11, article no. 11, pp. 17, 2014. View Article
[24] M. Stensberg, Q. Wei, E. McLamore, D. Porterfield, A. Wie, and M. Sepúlveda, “Toxicological studies on silver NP: challenges and opportunities in assessement, monitoring and imaging“, Nanomedicine, vol. 6, no. 5, pp. 878-898, 2011. View Article